
- #QUICKBOOKS PREMIER CONTRACTOR 2017 CRACKER#
- #QUICKBOOKS PREMIER CONTRACTOR 2017 MANUAL#
- #QUICKBOOKS PREMIER CONTRACTOR 2017 FULL#
- #QUICKBOOKS PREMIER CONTRACTOR 2017 PRO#
I can share some information about tracking inventory in QuickBooks Desktop (QBDT).
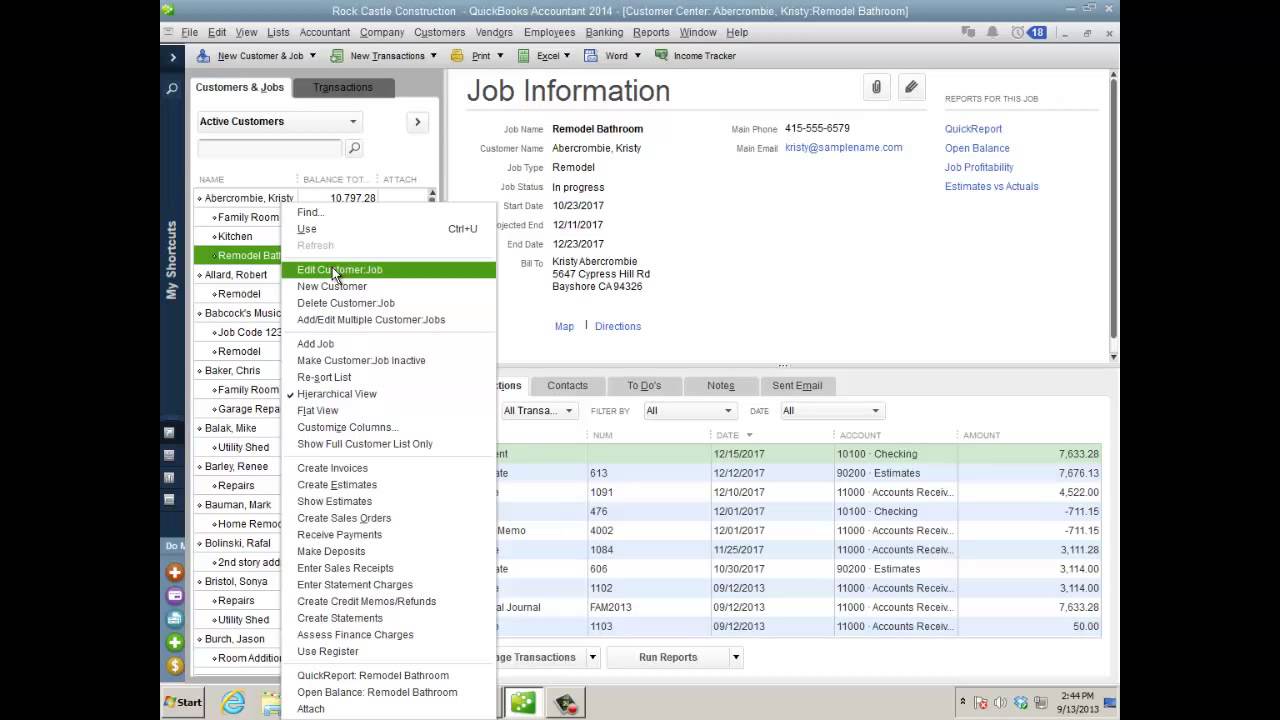
Greetings, for joining this conversation. When you do that, QB makes the required entries for income AND COGS - you do not have to make double sided items. You use that item on a sales receipt or invoice to sell it
#QUICKBOOKS PREMIER CONTRACTOR 2017 CRACKER#
The stocks the inventory item cracker with qty and cost per each.
#QUICKBOOKS PREMIER CONTRACTOR 2017 FULL#
Use write checks on the WIP bank account, do not print the check it is just used for data entry, select any vendor or create a dummy for this purpose, list your cracker item, enter the qty you actually made, and in the total item cost block enter the full amount in the wip account, save. Make your crackers in real life, when you know how many you have that can be sold Use inventory adjust, set the adjusting account to the WIP bank account and lower the qty of the item you will use - that moves the cost of the items to the wip bank. You can use a work around, but it is a painīuy and stock your inventory items, no you do not stock water that is a utility you pay for and is expensed already.Ĭreate a bank type account called work in progress (WIP) Then in build assemblies you build 100 of the cracker assembly. decimals like 0.125, 0.5 are fine, but a decimal of 0.33 or 0.85 is not. And it gets worse, you can use a decimal amount that does not add to one or inventory goes way off. so if you use 10# of flour to make 100, you need to stock the flour in ounces and calculate how many ounces it takes to make one cracker. If you choose to do so (which means buying premier), keep in mind that an assembly item makes one of something. If you can say that a measured amount of each ingredient always makes exactly 100 crackers with no waste, and no broken ones, then you might be able to use an assembly item - but I would not. a number of different things make one of something, each and every time, no waste no variable outputs.
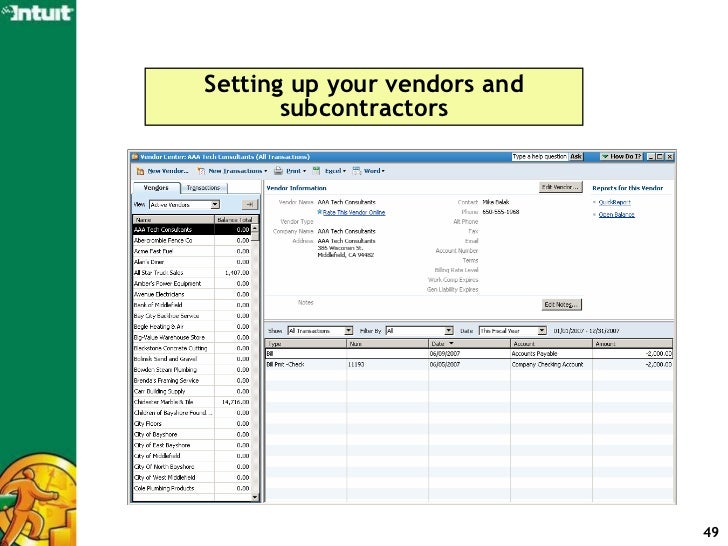
In QB an assembly item is a finite relationship.
#QUICKBOOKS PREMIER CONTRACTOR 2017 PRO#
This is a wasted explanation since you marked this as using pro - pro does not have the assembly item. There is no required inventory valuation or tracking method, periodic and perpetual are both fine and accepted Gaap is not a required standard unless you are listed on the market and subject to the SEC regulations, and the IRS does not accept all of the so called gaap standards. And you never use inventory asset in a transaction of any kind either. You do not, ever, use a journal entry for inventory or inventory items - never. Do not set up a second inventory account, there is no reason to, and it usually leads to problems and issues later on.
#QUICKBOOKS PREMIER CONTRACTOR 2017 MANUAL#
Your approach works in manual accounting using journal entries, but it does not work in QB if you use inventory Presidentĭo not create a balance sheet account called inventory - QB did that for you and it is a special type of account that QB likes to use. This Generally Accepted Accounting Principle results in maintaining a perpetual inventory system rather than a periodic system where you have to adjust purchases and inventory at the end of the rh Cash debit, Sales credit, along with the following entry Inventory credit, Cost of Sales Debit.

When you sell a given product the entry will be a double sided entry. Your purchased inventory needs to be posted to a GL Account called Inventory in the Balance Sheet.

Keep in mind you do not want to record your purchases in Cost of Sales. You will need to assign the sales amount. The cost of the packaged product will be the accumulated costs of all product used in your assembly. I would define the inventory card and set up a separate GL account for Finished Goods Inventory thereby separating your raw material inventory from your finished goods product. Set up an assembly for the recipe including the packaging and a new inventory item for the packaged crackers, either by package, box or carton however it comes off the line. Each component would be an inventory part. Have you set up an Assembly for each type of cracker you produce? That would be the best way.
